轉爐煉鋼動態控制技術
瀏覽:次|評論:0條 [收藏] [評論]
摘要:介紹了國內外轉爐煉鋼中用于過程動態控制的副槍和爐氣分析系統技術,并對國內大、中型轉爐終點采用動態控制技術提出了建議。
關鍵詞:轉爐;煉鋼;動態控制
1 轉爐吹煉控制技術的發展及現狀
自1952年世界上第一座氧氣轉爐在奧地利Doawitz廠投產以來,由于其生產效率高、產品質量好,得到迅速發展。從20世紀50年代到70年代主要是完善技術和實現大型化,70年代從靜態控制向動態控制發展,80年代以來,隨著計算機技術的全面推廣以及各種檢測手段的迅速發展,國外先進鋼鐵廠逐步研究采用計算機對轉爐吹煉進行控制,日本在80年代后開始采用全自動控制技術。國內除寶鋼、武鋼、首鋼等少數轉爐采用動態控制外,大多數轉爐的裝備、控制水平還較低,處于經驗控制向自動控制的過渡。
轉爐吹煉控制技術的發展可分為三個階段:靜態控制、動態控制和轉爐全自動吹煉控制。
1.1 靜態控制技術
靜態控制指轉爐吹煉前,根據初始條件和終點要求對轉爐吹煉過程進行模型計算制定出吹煉方案(提供供氧時間和各種輔原料加入量),以達到基要命中目標值,它可以對轉爐吹煉過程的熔池溫度和成分變化進行預報。
靜態模型是轉爐實現動態控制和全自動控制的基礎,轉爐要進行動態控制或全自動控制,必須首先建立靜態模型。但是,由于靜態模型不能根據吹煉情況采集爐內金屬液成分和溫度變化等爐內信息來調整吹煉參數,因此命中率較低。
1.2 動態控制技術
轉爐所采用的動態控制技術主要有副槍動態控制和爐氣分析動態控制以及副槍 爐氣分析動態控制。
1.2.1 副槍動態控制技術
副槍動態控制技術是在吹煉接近終點時(終點前2~3min),向熔池內插入副槍,檢測熔池溫度T和碳含量[C]及鋼水氧活度,并取出金屬樣。根據檢測數據,修正靜態模型的計算結果,計算命中終點所需的供氧量(或供氧時間)和冷卻劑加入量,調整后2~3min的吹煉參數。副槍安裝的組合探頭不同,具備的檢測功能也不同,終點命中率也不同。
1)寶鋼煉鋼廠。寶鋼一煉鋼、二煉鋼轉爐均采用計算機動態煉鋼技術,主要依靠所裝備的副槍檢測吹煉過程中鋼液的信息,通過動態控制模型對吹煉終點進行控制。
寶鋼的轉爐動態代數模型是根據副槍快速測定的結晶碳及鋼水溫度,分別利用指數函數及線性函數來推定吹煉停止時的鋼水碳含量和溫度,它還具有動態學習功能,即利用吹煉停止時的鋼水碳含量和溫度信息對動態模型參數進行校正,以提高下一爐的精度。據了解,終點一次命中率為80%-85%(控制精度:[C]士0.015%、T士13℃),補吹率在10%以下。
2)武鋼三煉鋼。武鋼三煉鋼是20世紀90年代新建的現代化煉鋼廠,轉爐靜態模型包括四相模型:即中間目標溫度計算模型、原料計算模型、熔劑計算模型和靜態計算模型。這四個模型決定每爐鋼吹煉前的設定值。轉爐冶煉在副槍第一次測量(占總氧耗量的85%左右)后進入動態控制,計算出達到目標溫度和目標碳所需的吹氧量及冷卻劑量,以后每吹氧3s,啟動一次動態計算,預測熔池內的碳含量和溫度,當溫度和碳含量都進入目標范圍時,發出提槍停吹指令。
從1997年下半年開始,通過對轉爐靜態模型參數和動態模型參數的優化調整,轉爐終點命中率(控制精度:[C]士0.01%,T士12℃)由開始的42.6%提高到2001年的平均93.1% ,其中2001年11月最高達到96.96%。補吹率一般在5%以下達到了國際先進水平。
3)濟鋼三煉鋼。濟鋼2000年新建投產的120t復吹轉爐采用了副槍和兩級自動化控制系統,副槍技術由達涅利公司提供,實現煉鋼過程的動態控制。所達到的轉爐一次命中率見表1。
表1 濟鋼三煉鋼120t轉爐終點命中率
[C]/% |
控制精度 |
[C]、T同時命中率/% |
0.02-0.06 |
[C]±0.015%,T±12℃ |
88 |
0.06-0.15 |
[C]±0.02%,T±12℃ |
84 |
0.15-0.24 |
[C]±0.03%,T±12℃ |
78 |
采用副槍測量實現了轉爐吹煉的動態控制,其優點在于:1)能完全消除轉爐初始條件波動的影響和系統誤差;2)基本消除吹煉過程中產生的隨機誤差;3)對終點進行近程預報,大幅度提高終點命中率。但轉爐副槍工藝只能提供吹煉過程中瞬時的碳含量和溫度,并不能提供連續的信息,嚴格來說,副槍仍然是一種靜態控制手段,只不過距終點時間很短,實質上轉爐生產的大部分時間仍是在靜態模型的指導下進行的。另外,副槍所采用的結晶定碳技術對低碳鋼的測量精度較高,而對高碳鋼的測量誤差卻較大。
1.2.2 爐氣分析動態控制技術
爐氣分析動態控制技術是通過連續檢測爐口逸出的爐氣成分數據,推算熔池瞬時脫碳速度和Si,Mn, Fe, P的瞬時氧化量,并對熔池物料平衡和能量平衡進行計算,求出熔池瞬時的升溫速度。它可依據前一時刻的檢測值,預報下一時刻的成分和溫度變化,同時,比較每一時刻的計算值與檢測值的誤差,不斷對結果進行校正,從而提高控制精度和命中率(如圖2-1、2-2所示)。
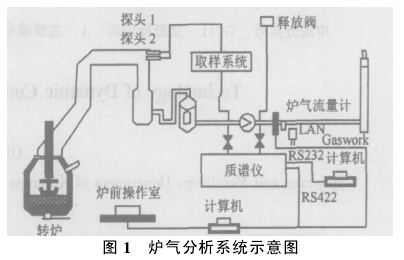

目前國外如歐洲、日本、韓國等有基于爐氣分析動態控制的應用實例較多,國內應用較少。據了解,在國內的大型轉爐中,目前只有本鋼、馬鋼一煉鋼己裝備了爐氣分析技術,攀鋼新建轉爐也將引進副槍 爐氣分析動態控制技術。
1)奧鋼聯(VAI)爐氣分析動態控制技術。奧鋼聯的轉爐爐氣分析動態控制系統由兩部分組成:①負責轉爐爐氣采集、處理和分析的低維護量的LOMAS系統;②轉爐二級動態控制模型DYNACON。可以分析溫度高達1800℃、煙塵含量高達100mg/m3的氣體成分。LOMAS系統由兩個氣體采集探頭、現場處理柜、氣體處理柜、控制柜和分析柜組成。
目前國內外鋼廠使用的爐氣分析技術多數是VAI提供的DYNACON動態控制模型和LOMAS系統。DYNACON的動態分析計算主要包括:①一次加料計算;②二次加料計算;③轉爐液面計算;④過程動態控制計算(核心部分);⑤補吹校正計算;⑥合金加料計算;⑦反饋計算。
在普通生產條件下,使用爐氣分析動態控制技術,碳的命中率可達到80%。如果能使供氧、底吹攪拌、吹煉方式、加料方式等進一步優化,可使命中率達到95%。同時可提高產品質量,降低生產成本。
2)中國馬鋼。馬鋼引進奧鋼聯的轉爐爐氣分析動態控制系統己成功應用于一煉鋼1座95t , 2座120t的頂底復吹轉爐上,是國內第一家引進該項技術的中、小型轉爐企業。該系統的硬件和軟件均從奧鋼聯引進(包括設計、安裝),2004年3月開始投入運行。
馬鋼一煉鋼的CSP和圓坯連鑄均配有LF爐,具有較強的溫度調節功能,因而對轉爐終點的鋼水溫度要求不嚴(高于1570℃即可),再加上轉爐冶煉的所有鋼種均為低碳出鋼,所以在爐氣分析系統投入應用后,轉爐冶煉CSP所澆鋼種及圓坯連鑄所澆鋼種時,基本可做到不倒爐直接出鋼,直接出鋼率在80%以上,從而使轉爐的冶煉周期由原來的40min縮短至目前的32 min。
馬鋼的爐氣分析系統應用較成功,所獲得的主要冶金效果:①縮短冶煉時間8min,使影響全連鑄節奏的限制性環節得到了解決;②縮短了高氧化性鋼水在轉爐內的停留時間,減少了爐襯的侵蝕,降低了耐材消耗;③深吹比例減少,鋼水、鋼渣的氧化性降低,脫氧劑及合金的用量減少。
爐氣分析動態控制技術的優點是:1)通過不斷地動態校正,可實現連續預報,提高控制精度;2)除預報熔池溫度和碳含量外,還可預報熔池的磷含量和爐渣成分的變化;3)適用于各種轉爐,不受爐口尺寸的限制,且成本低于副槍。
爐氣分析動態控制技術的不足之處是:1)爐氣分析只適用于低碳鋼吹煉終點控制。對于普通鋼種,采用爐氣分析動態控制可以取代或部分取代副槍測試,降低生產成本,但對于特殊鋼種或新開發的鋼種,為了得到直接和精確的測量結果,通常應該采用副槍;2)爐氣分析是通過連續檢測轉爐的爐氣成分來推算冶煉終點,屬于間接測量法,其測量精度受諸多因素的影響。比如:爐氣分析設備的分析精度、對爐氣流量的校正計算準確性、爐氣分析系統的響應時間、模型本身的精度等對控制效果影響較大;3)采用質譜儀在控制吹煉溫度方面尚沒有取得大的突破。
1.3 副槍 爐氣分析全自動吹煉控制技術
爐氣分析與副槍是檢測轉爐吹煉信息的兩種手段,以達到優勢互補,目前日本和德國的做法是在大型轉爐上同時采用副槍和質譜儀檢測,計算機采集數據在線計算,將結果指令連續下達給控制系統,實現完全自動控制,吹煉結束直接出鋼。
1)日本住友金屬。住友公司鹿島廠基于副槍檢測 爐氣成分分析,開發出具有參數自整定功能的終點控制系統。該系統包括動態控制模型和反饋計算模型,其中反饋模型基于副槍檢測結果分析動態模型的誤差趨勢,并根據相應的規劃確定反饋量,從而達到調整動態模型誤差的目的。另外,為了避免不正常操作的影響,相應開發出一個專家系統,根據經驗調整靜態模型。
2)日本神戶制鋼。日本神戶鋼鐵公司加古川鋼廠采用全自動吹煉控制240t LD/OTB轉爐,取得很好效果。其控制技術的主要特點是:①根據初②判始條件和終點目標,用靜態模型制定吹煉方案;采用氧槍加速度儀測量吹煉過程中的爐渣液位斷化渣情況,動態調整槍位和氧流量,控制吹氧和造渣過程,避免噴濺;③連續檢測吹煉過程中的爐氣成分,全程在線預報熔池C, Si, Mn, P, S含量和熔池溫度;④近吹煉終點時,用副槍測溫,進行動態校正,確定吹煉終點。
采用全自動吹煉技術后,能得到理想的控制效果:①減少噴濺,冶煉高碳鋼噴濺率從40%下降到8% ;②減少補吹次數,冶煉高碳鋼補吹率從1.4次/爐下降到1.1次/爐;③冶煉高碳鋼縮短冶煉時間10min,提高終點控制精度(見表2)。
表2 終點控制精度比較
成分/% |
副槍控制 |
全自動控制 |
P |
0.00249 |
0.00145 |
S |
0.00102 |
0.00093 |
Mn |
0.0165 |
0.0093 |
2 建議
近年來國內煉鋼廠在引進或改造轉爐時,都在考慮采用動態控制技術,副槍動態控制屬成熟技術,國內外用戶多,其使用效果穩定。相比較而言,爐氣分析技術在國外,特別是歐洲和日本應用很廣泛,但在國內應用并不多。具體采用何種技術,應根據轉爐大小、所煉鋼種要求、冶煉方法等諸多因素綜合考慮:
1)保證穩定的頂底復吹。動態控制模型,特別是爐氣分析動態控制模型要求轉爐必須具備良好的底吹條件,模型才能進行準確計算,才能實現系統的動態控制。如果底吹不正常,整個動態模型誤差較大,變成了靜態控制模型。因此在使用動態控制模型進行自動化煉鋼之前,必須保證轉爐能全程頂底復吹。
2)選擇合適的爐氣取樣點。要利用好爐氣分析儀,爐氣分析系統的響應時間非常重要。由于整個系統的響應時間受爐氣清洗系統的布置位置的限制,因此選擇好合適的氣體取樣點對最終效果關系很大。
3)穩定原材料并完善原料的計量檢測手段。必須使原材料及操作工藝實現標準化,如鐵水、半鋼的成分、溫度、廢鋼成分、尺寸、石灰、礦石等要有具體標準,并且要穩定。同時必須為轉爐配齊必要的控制裝置和計量檢測器具及儀表,并要保證其靈敏度與精度,完善計量檢測手段。
4)統一副槍和爐氣分析動態控制模型。迄今為止,國外己有不少鋼廠采用副槍 爐氣分析技術,但國內還無先例。采用該復合技術除要求兩套系統能獨立穩定運行外,統一考慮副槍和爐氣分析模型也是保證轉爐終點控制效果的重要因素。
3 結語
氧氣轉爐煉鋼技術問世50多年來,裝備水平和控制技術己經成為當今轉爐煉鋼廠技術進步的重要標志,副槍和爐氣分析是當今國內外眾多先進轉爐鋼廠為提高轉爐終點控制水平所采用的最有效的技術之一。通過引進、消化、一次開發轉爐終點控制技術,將不斷提升我國的轉爐冶煉工藝整體水平,使我國轉爐煉鋼終點控制水平達到一個新的高度。
- 上一篇:Quantum系列在煉鋼除塵上的應用 下一篇:采用副槍在線控制轉爐爐渣
- [騰訊]
- 關鍵字:無